The extrusion process is used to produce different forms of parts and components that are vital to industrial projects using various types of materials. A common form of extrusion is channels that are long pieces of metal that have the shape of the letter U as part of their structure. Read More…
Serving the aluminum extrusions world from Cleveland, Ohio, Talan Products specializes in a range of aluminum extrusion products and services.
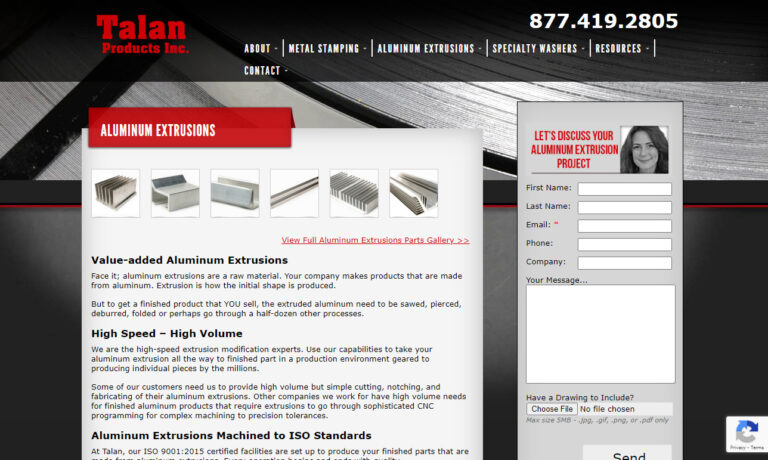
Quality Stamping & Tube Corp has been a leader in the aluminum extrusions and metal stamping industries for over 40 years. We attribute our success to our in-house die-making capabilities and wide range of extruded parts. All of our products are manufactured with quick turnaround and made to be high quality and durable. Our aluminum extrusions follow guidelines of up to 6 inches in diameter and...
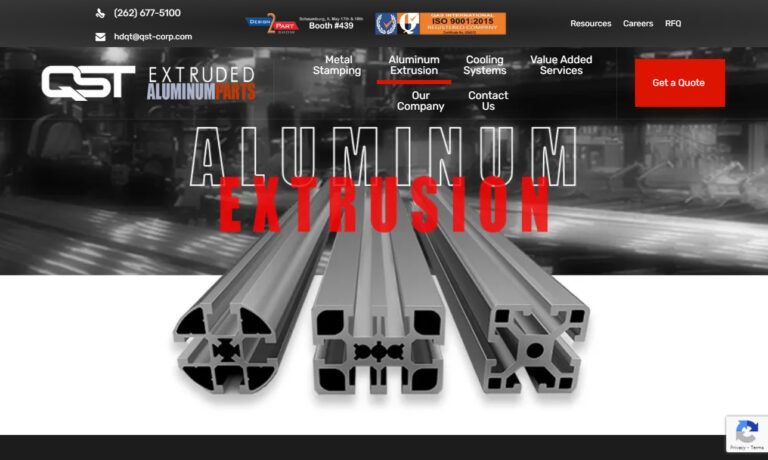
Since 1986, GSH Industries has offered on time delivery and competitive pricing. With over 40,000 square feet of manufacturing, we offer aluminum extrusion products and services.
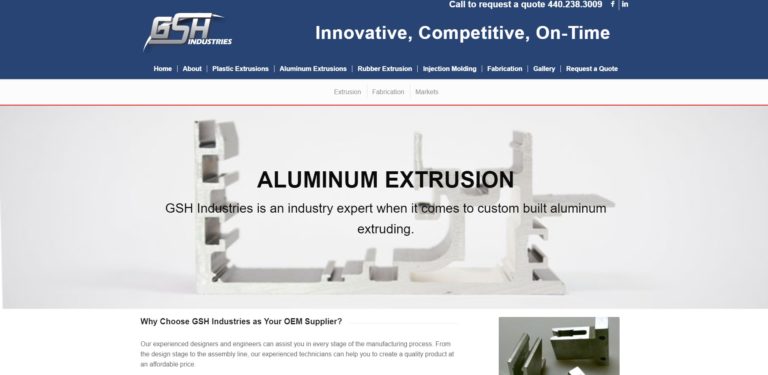
Dajcor Aluminum is the leading North American supplier of extruded, fabricated/machined, anodized and assembled components to the automotive, renewable energy, transportation, rail, marine, building trades, military, medical architectural and wall partition systems, office furniture, emergency vehicle and consumer product industries. Dajcor is an aluminum extrusion company with complete value add ...
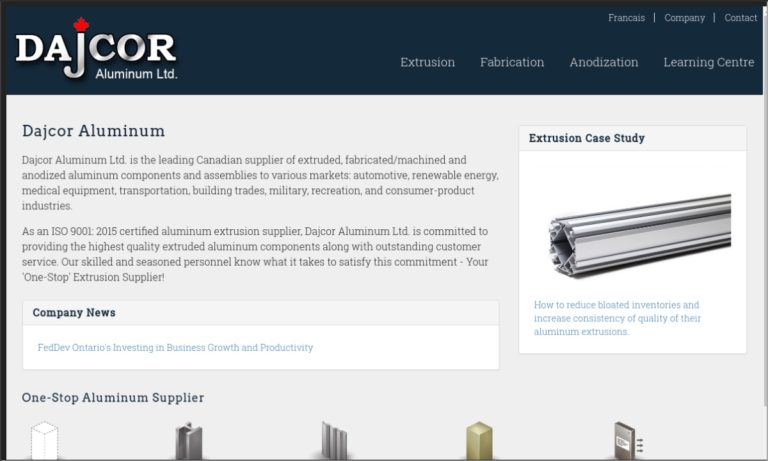
More Aluminum J Extrusion Manufacturers
The different forms of U channels include I beam types, U shapes, J channels, H channels, Z channels, and F channels, with each form being identified with a letter of the alphabet.
A special type of channel is J extrusions or J channels that are used to seal off edges and give a decorative finish to interior designs and construction projects. The term J extrusion or J channel refers to the shape of the channels that have the form and shape of the letter J with a long side and short side that are separated by a channel at the bottom of the J shape.
J extrusions are made from copper, steel, and other metals with aluminum being the predominant metal used due to its corrosion and rust resistance and its ductility. Aluminum is divided into series that begin with series 1000 and extend to series 8000. The difference between the series is in regard to the hardness of the aluminum with series 1000 being close to pure aluminum and very soft while series 8000 is alloyed with several metals that increases its hardness and strength but diminishes its resistance to corrosion.
The three grades of aluminum that are used for the production of J channels are grades 6061, 6063, and 7075, which have the necessary hardness and strength for use as structural components. There is a wide range of other aluminum grades that are used to produce J channels that are used in place of 6061, 6063, and 7075 that are selected for properties that fit the requirements of an application.
Series 6000 Aluminum
The factor that distinguishes aluminum series 6000 from other series of aluminum is its magnesium and silicon content, which gives series 6000 aluminum its extrudability, strength, weldability, machinability, and exceptional corrosion resistance. In addition, series 6000 aluminums can be heat treated to further increase their strength. Of the various grades of series 6000 aluminum, 6061 and 6063 are two of the most widely used grades of aluminum for a wide range of projects and applications.
The combination of magnesium and silicon produces magnesium silicide, a factor that enables 6000 series aluminums to be heat treated. The alloying of magnesium and silicon makes series 6000 aluminums more versatile, even though the various grades of the series do not have the strength and capabilities of series 2000 and 7000.
Grade 6061
Grade 6061 has a magnesium content of 1% with a silicon content of 0.6%. This alloying combination gives grade 6061 resistance to corrosion, stress, and cracking. The strength of 6061 is one of the reasons that it is used for the manufacture of J channels. The percentages of magnesium and silicon in grade 6061 makes it less malleable than other 6000 series aluminums, a factor that necessitates the use of substantial force to cold work grade 6061.
Although grade 6061 is difficult to cold work, it has good formability when annealed, which makes it possible to extrude it. After extrusion, 6061 is normally heat treated to increase its strength. The discovery of 6061, formally known as Alloy 61S, was an attempt to produce an aluminum grade that had mechanical properties and was weldable. After its discovery, 6061 became one of the most commonly used aluminum alloys.
Grade 6063
As with grade 6061, grade 6063 is a widely used aluminum grade used to produce complex shapes, configurations and products. Since it can be anodized to produce pleasing colors, grade 6063 is referred to as the architectural aluminum for window framing, door frames, roofs, and sign frames, which is a common use for J channels. The mechanical properties of 6063 are dependent on how it is tempered to create alternate grades 6063-T1, 6063-T4, 6063-T5, and 6063-T6.
The different types of tempering increase the tensile strength of aluminum grade 6063 to as much as 190 MPa or 28000 psi. The strength derived from the tempering further varies in accordance with the thickness of the aluminum being treated. When aluminum grade 6063 is welded, the properties near the weld take on the properties of grade 6063-O that has a tensile strength of 130 MPa or 19000 psi.
Series 7000 Aluminum
The principal alloying agent of series 7000 is zinc that is combined with small amounts of magnesium. As with series 6000, the result of the alloying is a heat treatable alloy with high strength with grade 7075 having the highest strength, which is used to produce J channels. To increase the hardness of series 7000 aluminums, they are precipitation hardened, a factor that makes them the highest strength commercially available aluminum.
Series 7000 aluminums are slightly tougher than series 6000 aluminums and are free machining metals. The increased strength of series 7000 makes it less ductile and less resistant to corrosion. When series 7000 aluminums are exposed to certain environments, they discolor and lose their appealing appearance.
Grade 7075
Grade 7075 is widely used for the production of J channels due to its high strength. It is commonly used in applications where high strength is required and corrosion resistance is not necessary. Grade 7075 is classed as a high strength aerospace aluminum alloy with exceptional stress corrosion resistance, which is the formation of cracks in corrosive conditions, a factor that can lead to failure when ductile metals are exposed to tensile stress.
The strength of grade 7075 aluminum is comparable to certain types of steel. This particular characteristic makes 7075 ideal for the manufacture of structural J channels but also lowers its machinability and weldability. Grade 7075 aluminum is chosen for applications that are under stress, such as aircraft wing spars and support equipment.
J channels produced using grade 7075 aluminum are used as high stress structural components. Regardless of its high strength and durability, Grade 7075 aluminum can be extruded into a wide range of forms, shapes, and sizes, as well as an assortment of angles.
Extruded J Channel Shapes and Forms
The term J extrusions or J channels covers a wide range of components that have the J shape, aside from the straight forward typical J shape with a long and short side with a channel in between. The main differentiation between the various types of J channels is the width of the channel portion of the J, which can be less than an inch or as much as several inches. This particular factor is in regard to the application for which the J channel is to be used.
The common uses for J channels are edging for windows, doors, and roofs and as support for mirrors and artwork with edging being the most common use, which provides a clean finished appearance. The extrusion of different grades of aluminum to form J channels is the most common method used for their manufacture due to the reliability and cost of the process.